Blog Article
Ensuring quality in the battery industry

Dr. Angelo Canzaniello
05.09.2024
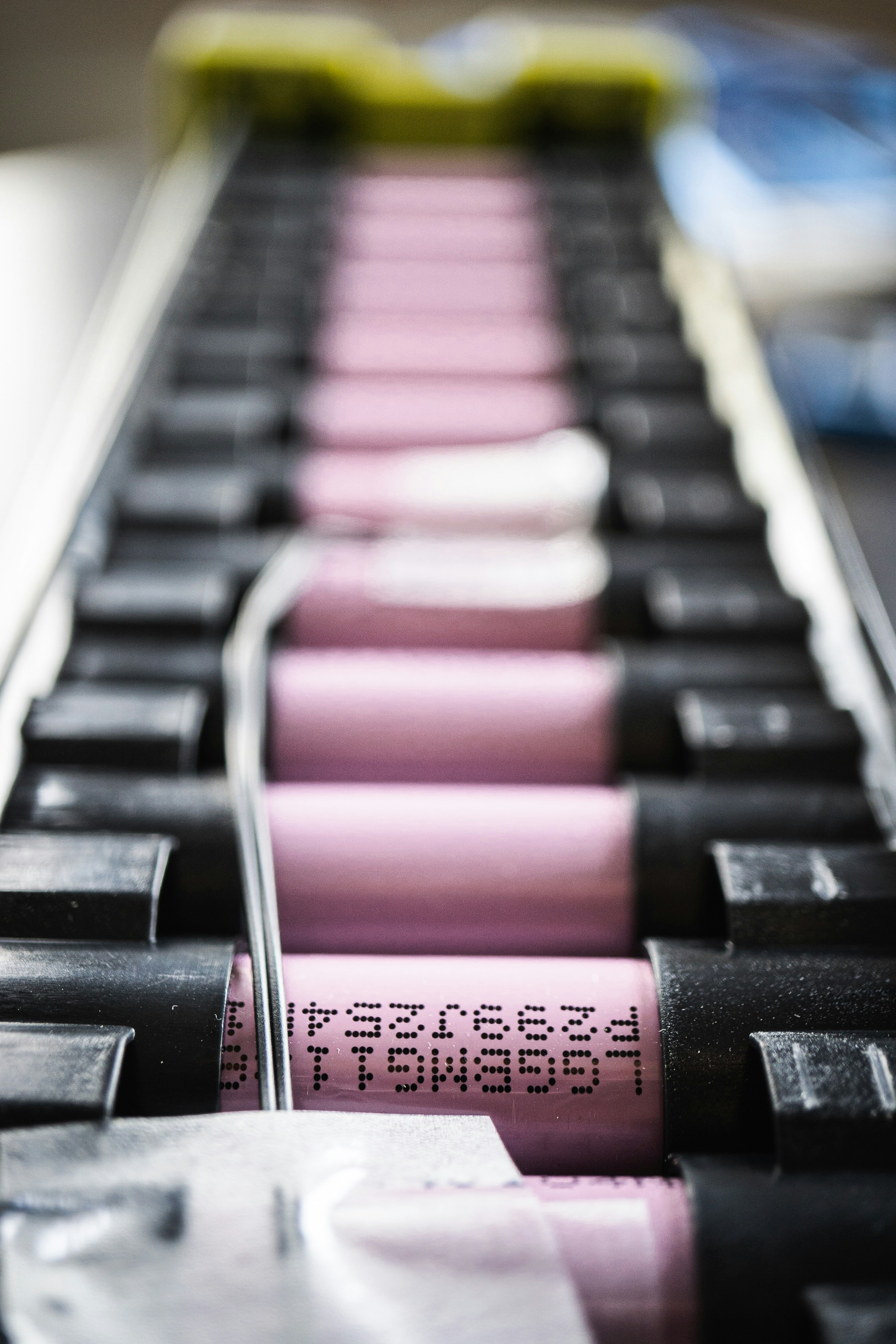
Quality Assurance in the Battery Supply Chain: Ensuring Safety and Reliability
In the rapidly evolving world of electric vehicles (EVs), consumer electronics, and renewable energy storage, the demand for high-quality batteries has never been greater. However, as battery technology advances and production scales up, ensuring consistent quality across the entire supply chain has become a critical challenge for manufacturers and suppliers alike.
Quality assurance (QA) in the battery supply chain is essential to guarantee that batteries meet safety, performance, and longevity standards, while also adhering to regulatory requirements. Without a robust QA framework, companies risk delivering faulty products that can lead to safety hazards, poor customer satisfaction, and significant financial or reputational damage.
In this blog post, we will explore the role of quality assurance in the battery supply chain, the challenges companies face in maintaining high standards, and the key steps involved in developing a comprehensive QA strategy.
Why Quality Assurance Matters in the Battery Supply Chain
At its core, quality assurance ensures that each battery produced performs as expected, withstanding the rigors of everyday use without compromising on safety. In industries such as EVs and energy storage, where battery performance is crucial, poor-quality batteries can have far-reaching consequences.
Safety Concerns
Batteries, particularly lithium-ion batteries, can pose significant safety risks if not properly manufactured. Poor quality control can result in overheating, short-circuiting, or even fires and explosions. Such incidents have been widely reported in consumer electronics and electric vehicles, damaging both consumer trust and brand reputation. Quality assurance helps identify and mitigate these risks before products reach the market.
Performance and Reliability
High-quality batteries ensure long-lasting performance and reliability, critical factors for electric vehicles, where battery degradation can significantly reduce driving range and consumer satisfaction. Similarly, in renewable energy storage, battery reliability is crucial for efficient energy management. Without stringent quality assurance, companies risk delivering products that fall short of their performance claims.
Regulatory Compliance
As global regulations around battery safety and sustainability tighten, compliance has become a vital component of any quality assurance strategy. Failing to meet regulatory standards can lead to product recalls, fines, and legal consequences, particularly in markets like the European Union, where battery regulations are becoming increasingly stringent. Quality assurance ensures compliance with these evolving regulations, helping companies avoid costly penalties.
Challenges in Quality Assurance
Ensuring quality across the battery supply chain is far from straightforward. Several factors contribute to the complexity of quality assurance in this space:
Complex and Fragmented Supply Chains
The battery supply chain involves numerous stages, from raw material extraction to cell manufacturing and assembly. Each stage has its own set of suppliers, standards, and processes, making it difficult to maintain a consistent level of quality. For instance, raw materials like lithium and cobalt are often sourced from regions with varying quality standards and levels of oversight, introducing variability that can impact the final product.
Lack of Standardized Testing
Different suppliers may use different methods for testing and ensuring the quality of materials and components. The absence of uniform standards across the industry can result in inconsistencies in product quality. While some manufacturers may adhere to rigorous testing protocols, others may cut corners to reduce costs or meet production deadlines, leading to subpar batteries entering the market.
Scaling Up Production
As the demand for batteries grows, especially with the rise of electric vehicles, scaling up production to meet this demand puts additional strain on quality control processes. The faster manufacturers ramp up production, the harder it becomes to maintain rigorous quality checks, increasing the risk of defects slipping through.
Technological Advances
Battery technology is constantly evolving, with new chemistries and designs emerging regularly. While these innovations promise better performance and energy density, they also introduce new challenges for quality assurance. Manufacturers must adapt their testing protocols to account for these changes, ensuring that new technologies meet safety and performance standards.
Key Steps in Building a Robust Quality Assurance Framework
To overcome these challenges, companies must develop a comprehensive quality assurance framework that spans the entire battery supply chain. Here are the key steps involved:
Supplier Audits and Certification
The first step in ensuring quality is to thoroughly vet and audit suppliers. This involves conducting on-site inspections of suppliers' facilities to assess their manufacturing processes, quality control protocols, and adherence to regulatory standards. Companies should only work with certified suppliers who meet industry standards, such as ISO 9001 (for quality management) or ISO 14001 (for environmental management). Building strong relationships with trusted suppliers helps reduce variability in the supply chain.
Standardized Testing and Quality Control
Implementing standardized testing protocols is crucial for maintaining consistency in battery quality. This includes testing for performance factors such as energy density, charge cycles, and thermal stability, as well as safety tests like overcharging, short-circuiting, and puncture resistance. Regular testing throughout the production process helps identify defects early, reducing the risk of faulty batteries reaching consumers.
Advanced Monitoring and Data Analytics
Many companies are turning to advanced monitoring systems and data analytics to enhance quality assurance. Technologies like AI and machine learning can be used to detect patterns and anomalies in the manufacturing process, allowing for predictive maintenance and real-time quality control. For example, sensors embedded in production lines can monitor temperature, voltage, and other variables, flagging any deviations from the norm that may indicate potential quality issues.
Collaboration and Transparency Across the Supply Chain
Ensuring quality requires close collaboration between all stakeholders in the supply chain. This includes sharing data on quality control practices, testing results, and production challenges between suppliers and manufacturers. Greater transparency helps align expectations and ensures that all parties are working toward the same quality standards.
End-of-Line Testing and Inspection
Even with robust in-process testing, end-of-line testing and inspection are critical. This final step ensures that the finished battery meets all necessary safety, performance, and regulatory requirements before it is shipped to the customer. Thorough visual inspections, performance tests, and random sampling help catch any defects that may have gone undetected during earlier stages of production.
Continuous Improvement
Quality assurance is not a one-time effort but an ongoing process. By regularly reviewing and improving their QA strategies, companies can adapt to new challenges, technologies, and market demands. This involves incorporating feedback from customers, conducting post-market surveillance, and continuously improving testing and manufacturing protocols.
Conclusion
In the fast-growing battery industry, quality assurance is more important than ever. From ensuring the safety of products to meeting regulatory standards, QA processes play a crucial role in maintaining customer trust, reducing risks, and delivering reliable and high-performing batteries.
As supply chains become more complex and demand continues to rise, companies that invest in comprehensive quality assurance frameworks—supported by supplier audits, standardized testing, and advanced monitoring—will be better equipped to navigate the challenges and seize opportunities in this dynamic industry. The future of energy storage depends not only on innovation but also on the consistent quality of the batteries that power our devices, vehicles, and infrastructure.
Power up your supply chain.
Get started now. Book a consultation with us.